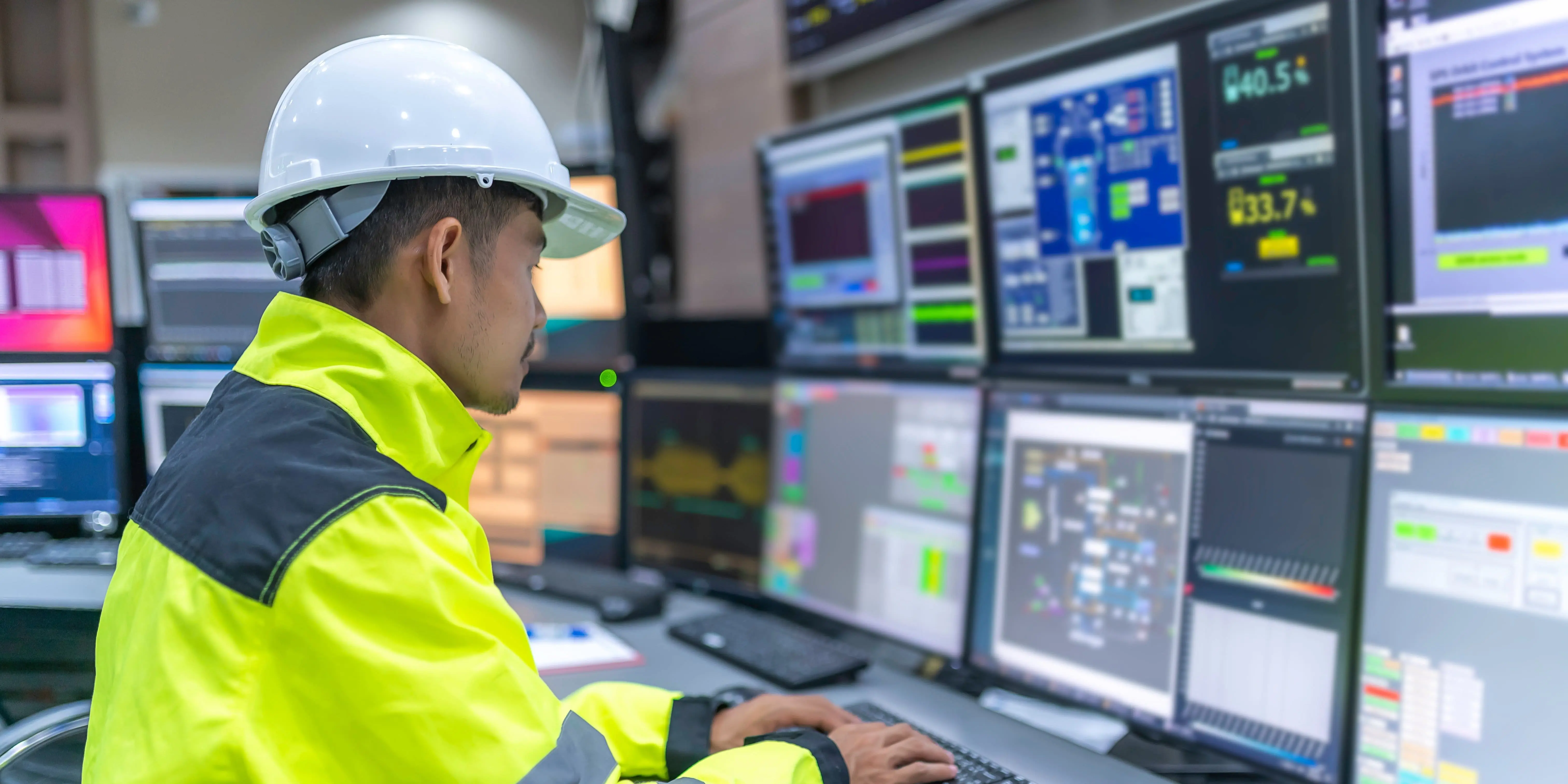
Condition-based monitoring is the process of collecting and analyzing information about the condition of electrical assets to identify potential problems before they lead to asset failures. Condition monitoring is widely acknowledged as the most cost-effective maintenance strategy since it eliminates the need for unnecessary inspection and upkeep.
The installation of condition monitoring sensors is used to track variables such as vibration and temperature for electrical equipment. The collected information, or data, is then sent to a computer, application, or cloud platform to be analyzed so that personnel can take the necessary actions to rectify anomalies.
The Industrial Internet of Things (IIoT), which uses the power of connected digital technology to guide maintenance routines, has helped to further this concept through the ability to improve the reliability, efficiency, and safety of electrical systems.
By implementing condition-based monitoring, organizations can realize several benefits:
1. Reduce maintenance costs: Lowering the cost of maintenance is one of the main advantages of condition monitoring. The ‘fix it when it breaks’ strategy is a corrective maintenance approach that allows assets to run to failure before repair or replacement must occur. Although using the fix-it-when-it-breaks approach can initially result in reduced expenses, the long-term costs are always higher. Unexpected asset failure is more expensive because it halts the operations that a predictive maintenance approach could otherwise prevent. Monitoring electrical assets in real-time helps reduce the cost of periodic checks because the real-time data provides continuous awareness of asset conditions and analytics for better asset monitoring and maintenance.
2. Maximize asset reliability to improve uptime: Asset performance and uptime increase when maintenance is performed at the right time. In most industries, any amount of downtime can have negative implications for the company, costing significantly more in reputation damage and production loss than the maintenance or replacement of the compromised asset. To reduce unplanned downtime incidents, it is important to have maintenance performed not only periodically but at the right time. It makes little sense to have maintenance scheduled for a week or a month’s time when an asset is about to fail and needs to be checked immediately. Condition monitoring predicts potential problems that can lead to failure before they occur. The ability to identify potential faults before a failure occurs helps to maximize operational uptime by avoiding power outages.
3. Monitor critical assets 24x7: Real-time asset monitoring provides continuous insights into system health. Monitoring assets in real-time gives 24x7 access to a constantly updating pool of information on your machinery, and provides valuable, real-time data for trend analysis. This alerts engineering teams to potential issues and enables prioritising maintenance tasks. Unlike reactive and planned maintenance, this helps to make informed decisions around scheduled maintenance, saving costs and time. Monitoring assets in real-time improves the efficiency and reliability of equipment by identifying potential flaws in asset health. This enables maintenance efforts to focus on those assets requiring early attention as opposed to reacting when the asset is already experiencing issues or worse, when an electrical power outage occurs.
4. Prioritize maintenance activities: When there is little or no insight to predict electrical asset health, personnel have limited ability to prioritize maintenance schedules. This forces them to operate on a ‘first-come, first-serve’ approach, scheduling maintenance activity using the ‘fix it when it breaks’ strategy. The ability to access real-time health status updates for electrical assets enables personnel to anticipate failures and plan for repair or replacement. This helps improve performance through the utilization of data insights and avoid unplanned outages that can result in downtime and production delays.
5. Increase asset lifespan: Many electrical assets are typically built to last for over 20 years provided regular maintenance intercepts faults. However, equipment still becomes damaged as a result of issues encountered during unexpected shutdowns, environmental conditions, and component degradation. These factors compromise asset integrity and shorten their lifespan. Condition monitoring helps by tracking equipment health during operations, alerting personnel when variables change in advance of component failure. This can extend asset lifespan and lower operational costs, mitigating the need to change the original equipment parts of an asset.
6. Improve personnel safety: Improving the safety of site personnel is an important benefit of condition-based monitoring. Sensors identify potential faults, which in turn helps limit the exposure of personnel to compromised assets that can present safety risks. Many types of mechanical failure can be hazardous and result in an arc flash, or worse, fires. With the installation of condition monitoring systems, personnel interaction with assets is minimized, reducing the need to physically engage with potentially hazardous equipment that requires checking.
7. Improve efficiency and productivity: Condition monitoring solutions have predictive capabilities that provide a data-led maintenance programme to enable the creation of more precise production planning. The implementation of a preventive maintenance strategy alerts operatives to the health of compromised assets before potential faults occur. This prevents faults from developing into something harmful, meaning organizations can increase their overall production using reliable real-time data to inform operational management. This has the positive side effect of improving customer satisfaction resulting from more efficient manufacturing strategies and accurate delivery predictions.
Condition-based monitoring enables asset digitalization and analysis. Through the ongoing collection and logging of condition data, condition monitoring powerfully contributes an organization's digitization activities. Continuous Thermal Monitoring (CTM) can play a key role in condition-based maintenance procedures for critical electrical distribution systems. By integrating remote condition monitoring technology into your organization's critical infrastructure today, you are taking steps towards the future by enhancing your digital preparedness and resilience.