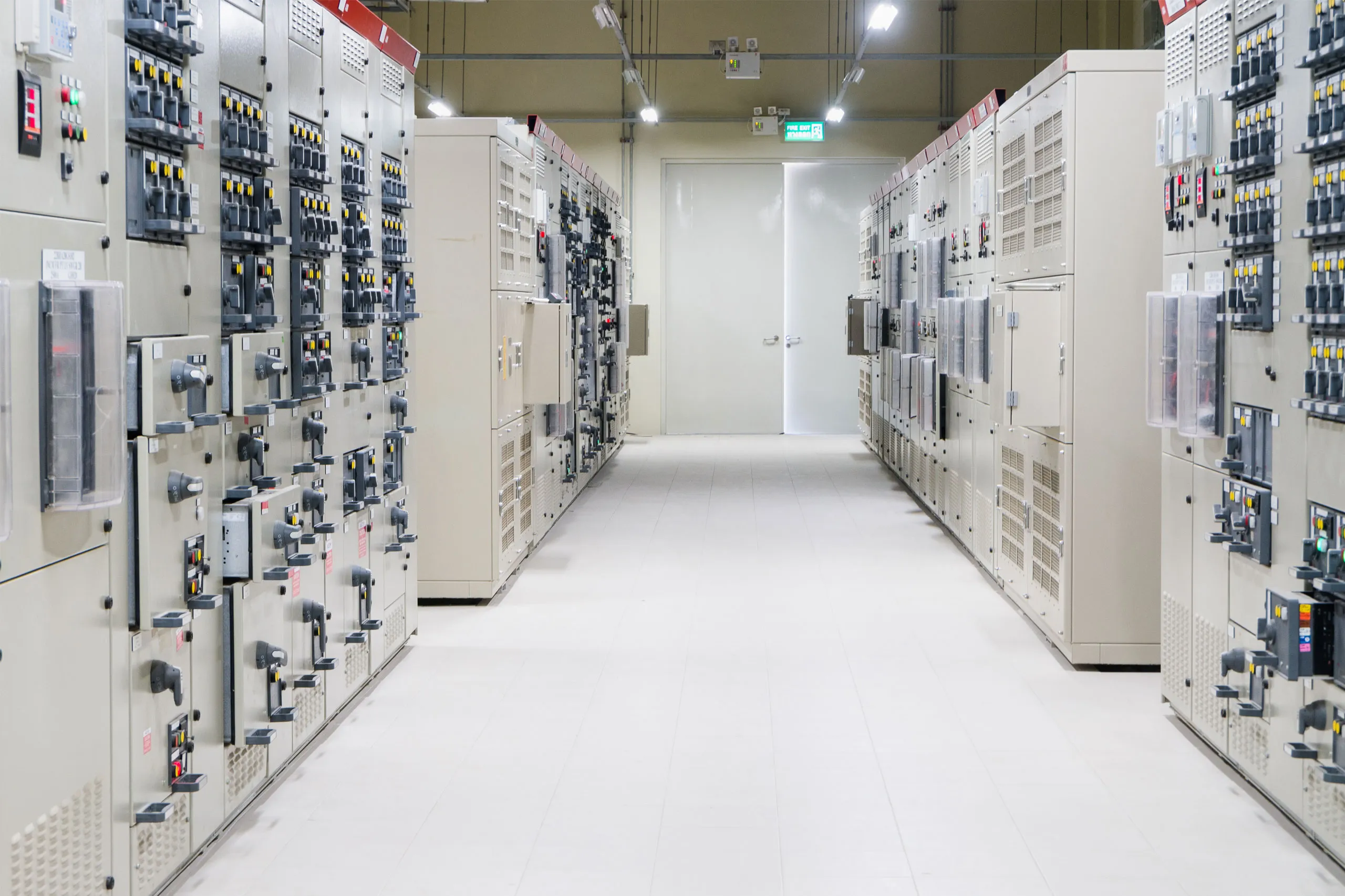
Switchgear is essential to electrical systems, but with the numerous challenges associated with failures, engineers must adapt to ensure power is distributed reliably to organizations. The adoption of maintenance strategies can help to prevent switchgear failures. This blog examines the causes of switchgear failure and introduces an innovative solution, continuous thermal monitoring, or CTM, that transforms electrical maintenance and provides a solution to switchgear failures.
What is switchgear?
Electrical switchgear refers to a collection of devices used in electrical systems to control, protect, and isolate a power system with multiple controls housed in a metal enclosure. Switchgear is an integral part of power transmission and distribution networks and helps ensure the safe and efficient flow of electricity.
Switchgear in an electrical power system is responsible for:
- Control: Using switches, breakers, or relays to permit or interrupt current passage to regulate the flow of electrical power.
- Protection: Keeping circuits and electrical equipment free from risks or damage caused by overloads, short circuits, and other abnormal conditions.
- Isolation: Preventing extensive disruptions and guaranteeing safety during maintenance or repairs by separating malfunctioning parts or equipment from the rest of the system.
Switchgear, such as circuit breakers, fuses, disconnect switches, and relays, can be categorized according to their function. Switchgear is available in various types and voltage levels, from low to high voltage. It is frequently found in power generator plants, substations, commercial buildings, and industrial facilities. Switchgear is essential to preserving the reliability and security of electrical networks.
Types of switchgear
- Low Voltage (LV) switchgear: Mostly used in several industrial or building settings for localized power distribution to regulate systems up to 1 kilovolt. It regulates power flow and protects circuits.
- Medium Voltage (MV) switchgear: Typically used in substations to control power transmission, this type of switchgear is designed for voltages higher than 1 kV.
- High Voltage (HV) switchgear: Provides dependability and fault protection by operating at extraordinarily high voltages for grid-level power distribution.