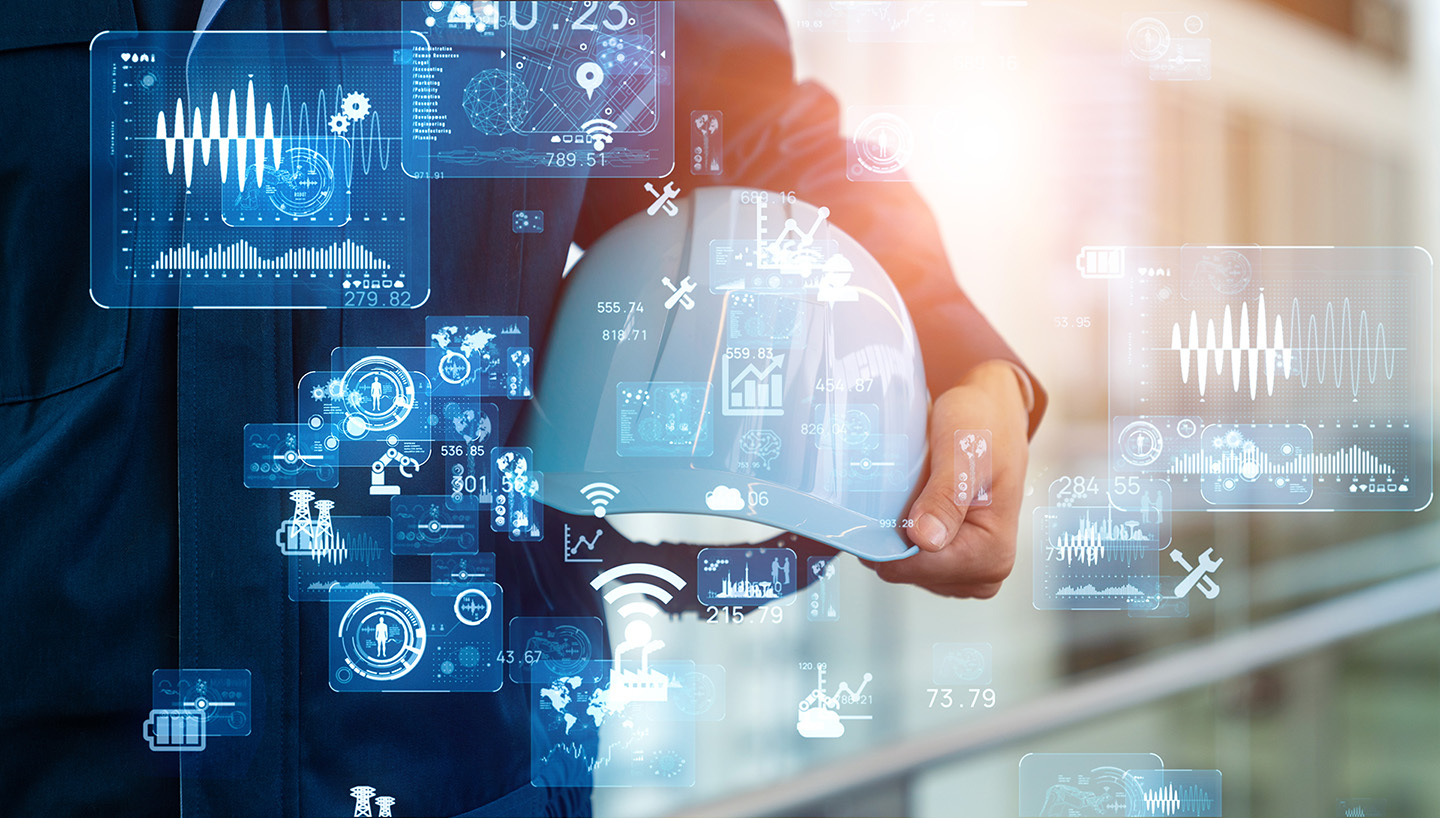
What is CMMS?
A computerized maintenance management system (CMMS) is a software solution designed to help organizations simplify and facilitate maintenance management operations. CMMS is described in a number of ways: Computerized Maintenance Management Information System (CMMIS); CMMS software; CMMS system; CMMS platform; or simply maintenance software.
CMMS is an advanced digital platform that serves as a centralized database for managing, monitoring, and analyzing the various elements of an operation, including planning, tracking, and organizing inventories and labor for equipment maintenance.
Optimizing maintenance procedures, extending asset lifespans, reducing operational expenses, and improving regulatory compliance are some of the key objectives of a CMMS in an organization. CMMS helps maintenance teams work more efficiently by centralizing data and automating maintenance management tasks. The fundamental component of a CMMS is its database. This frees up resources for strategic initiatives and preventive maintenance instead of being consumed by labor-intensive, manual operations.
How does a CMMS work?
The primary purpose of a computerized maintenance management system (CMMS) is to increase the visibility of maintenance management for teams and, as a result, improve the efficiency of an organization.
CMMS helps improvement in a number of areas, including:
- Data centralization: Fundamentally, CMMS establishes a single, centralized database for assets, equipment, inventory, and maintenance procedures. Work orders, maintenance schedules, location, warranty details, inventory, assets, equipment, and historical maintenance data can all be included in a centralized database. Organizations can remove data silos through broad team accessibility of the software platform, offering permission to suit personnel requirements. This enables the right level of information access for all stakeholders that need to make informed decisions by establishing a single source of truth.
- Maintenance scheduling and planning: The proper planning and scheduling of preventive and corrective maintenance tasks is improved by CMMS. Preventive maintenance operations are scheduled based on predetermined intervals or usage triggers to maintain regular asset upkeep and reduce the risk of unplanned asset failures. Corrective maintenance is also used to deal with any unforeseen problems. Based on these schedules, the system may automatically create work orders, guaranteeing that maintenance tasks are completed on time and resources are correctly optimized.
- Material and inventory management: The inventory of replacement parts and supplies required for maintenance jobs is managed by CMMS. It sets reorder points, automates the buying process, and keeps track of inventory levels. Aside from reducing downtime and unnecessary stock-holding expenses, effective inventory management guarantees that parts are available when needed.
- Work order management: When preventive or corrective maintenance is required, CMMS makes it easier to create work orders. These work orders specify the tasks, the resources needed, equipment and parts, and the designated workers. Workflow and job prioritization are enhanced when maintenance personnel receive notifications and can update the status of work orders in real-time.
- Reporting and analysis: Comprehensive reporting and analytics tools that give insights into asset performance and maintenance operations are provided by CMMS. Organizations can generate reports on various parameters, including maintenance costs, downtime, asset lifespan, and schedule compliance. These insights help with trend identification, decision-making, and the ongoing improvement of maintenance strategies.
- Mobile accessibility and integration: The mobile accessibility of many modern CMMS solutions allows maintenance staff to use mobile devices to access the system, check work orders, and change task status from any location. CMMS can also be integrated with other systems for improved operational efficiency and smooth data transmission, including Enterprise Resource Planning (ERP) systems.