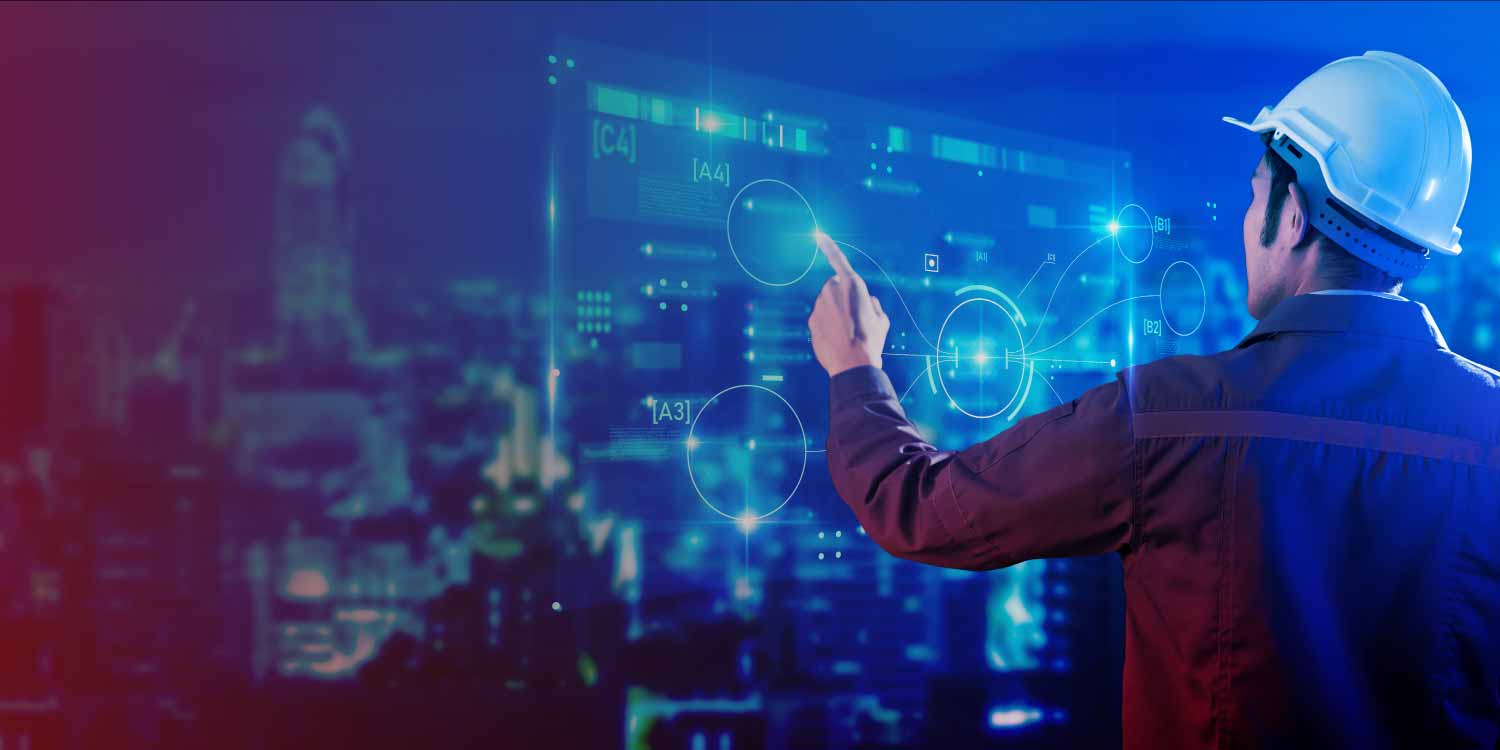
The unstoppable march of Industry 4.0, Big Data, and the Internet of Things pushes organizations to accumulate the essential data they need to perform at the highest level. McKinsey estimates that IOT has the potential to unlock an economic value somewhere between US$5.5 to $12.6 trillion by 2030. But what does this mean for electrical asset managers, and how can they respond to the call to upgrade systems in an increasingly complex and globalizing world with supply chain challenges?
This article explores the concept of condition monitoring for organizations and how it can help electrical personnel take steps to digitize critical electrical components to become more future-proofed. We'll uncover how thermal sensors play a vital role in monitoring crucial electrical infrastructure, where the advantages of the technology extend far beyond the extraction of essential data.