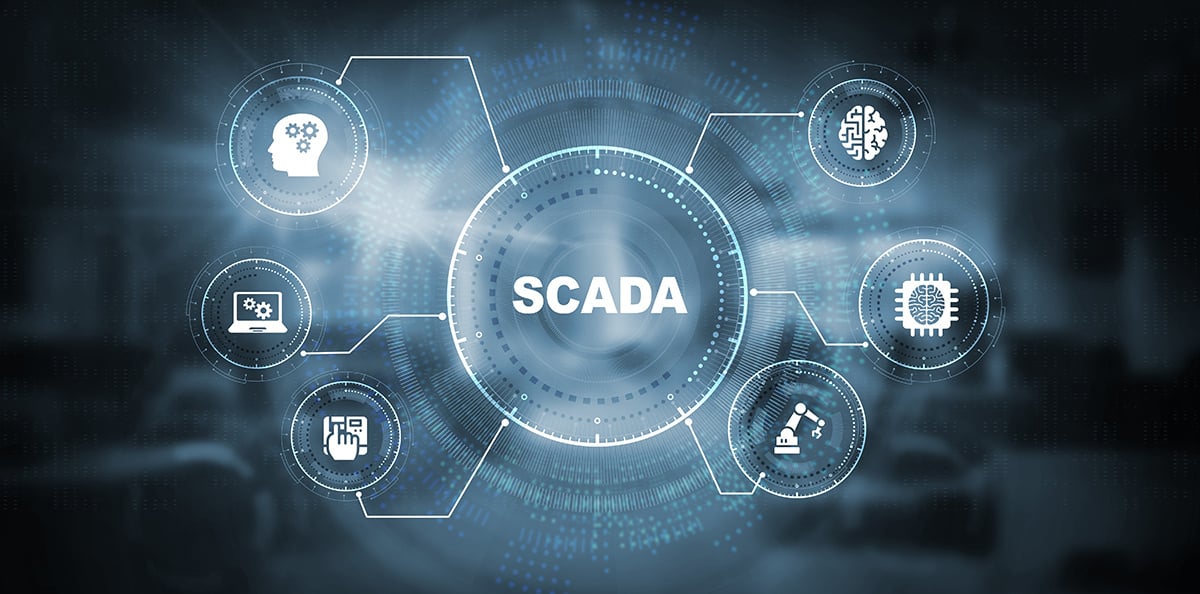
What is SCADA?
Supervisory Control and Data Acquisition, commonly known as SCADA, is an automated control system used in modern electrical systems to help drive more efficient operations. SCADA systems are designed to collect data from critical assets via sensors installed within equipment across an organization. Data can be processed and analyzed, and the output can be used to enable personnel to make, better, more informed decisions about the best course of action with their assets.
SCADA systems consist of software and hardware components that enable operators to gather data to efficiently monitor, control, and optimize electrical assets. These systems provide remote control for equipment monitoring processes, performance aberrations, and data analysis.
How does SCADA work?
Communication networks are the backbone that connects components such as sensors, RTUs (Remote Terminal Units), PLC’s (Programmable Logic Controllers), and the central controls in SCADA systems. These communication networks ensure data flows seamlessly between field devices and peripheral systems, enabling real-time monitoring and control.
Operational efficiency and electrical asset reliability are enhanced when a SCADA system is connected to equipment. The system can collect varying types of data from equipment, including temperature, pressure, or speed data. The data may then be analyzed and presented in a dashboard, and trends can be determined.
Such insights may then be used to take broader actions, allowing personnel to make better decisions.
A typical SCADA system will comprise several components, which include:
- Sensors and Actuators: Sensors provide the necessary data from measured parameters like pressure, flow, voltage, temperature, and so on for monitoring, while actuators receive control signals from the sensors to enable automated control capabilities for operational adjustments and optimization. These are crucial components of SCADA systems for real-time feedback on process performance.
For example, if a sensor detects a high temperature trend, an actuator can be triggered to turn on a cooling system.
- Remote Terminal Units (RTUs): RTU’s collect real-time data from sensors connected to their input modules and forward the processed data to the central SCADA system over the preferred communication channel. This data is forwarded regularly or when significant changes occur, ensuring the central control system has up-to-date information.
- Programmable Logic Controllers (PLCs): PLC’s allow direct control of machinery and processes based on sensor data. The PLC receives control commands from the SCADA system based on processed data, which then adjusts the actuator's control actions to make the necessary changes, such as opening or closing valves, starting or stopping motors, or adjusting flow rates.
For example, if the SCADA system detects an anomaly or a need to make an adjustment, it sends signals to the PLC that trigger relevant actuators to make the necessary changes.
- Communication Networks: Networks connect the sensors, RTUs (Remote Terminal Units), PLC’s, and the central control system. These networks allow for remote monitoring and a seamless flow of data between field devices and the SCADA system, enabling real-time monitoring, control, and automation of industrial processes. In other words, communication networks facilitate data collection, transmission, processing and display, control commands, and action implementation.
- Human Machine Interface (HMI's): These are the user interfaces or dashboards that enable personnel interaction with a machine, system, or device with data visualization and trend analysis of the various monitored and controlled processes. HMI's also provide real-time visual or audible notifications when process parameters deviate from the predefined acceptable range.
Automated reports on system performance can be generated by HMI’s that could be scheduled or triggered by defined events.