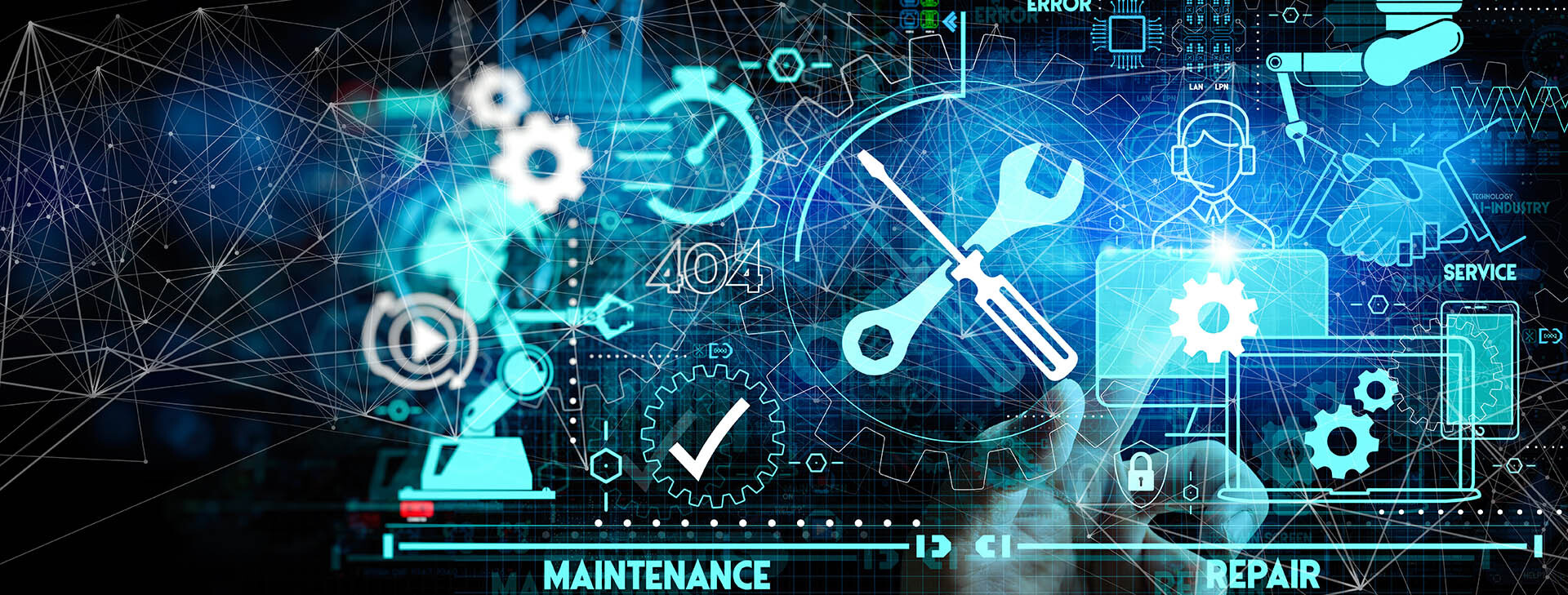
What is routine maintenance?
Routine maintenance, also known as scheduled maintenance or periodic maintenance, is a maintenance approach to keeping machinery, systems, and equipment in good working condition by carrying out routine cleaning, inspection, and repairs at arranged times.
Routine maintenance is a preventive maintenance approach that is implemented to prolong equipment lifespan, ensure it operates at peak performance, and safeguard against unplanned malfunctions and downtime. Equipment maintenance schedules can be set by timed cycle (e.g., monthly, quarterly, or yearly) or consumption (e.g., after 10,000 hours of operation).
The main objective of routine maintenance on electrical assets is to identify and fix problems before they escalate to something that could cause equipment failure, costly repairs, and downtime. Organizations can benefit from this approach by following a regular maintenance schedule. These benefits include better safety conditions, increased equipment performance, resource optimization, and reduced long-term costs.
Examples of routine maintenance:
- Periodic inspection: Looking for indications of deterioration, damage, or other possible problems.
- Cleaning: Eliminating impurities such as dirt and debris that may hinder performance.
- Lubrication: Putting lubricants on moving parts to lessen friction.
- Adjustments: Making the required changes to guarantee the best possible performance.
- Parts replacement: Replacing worn-out or damaged parts in advance of their failure.