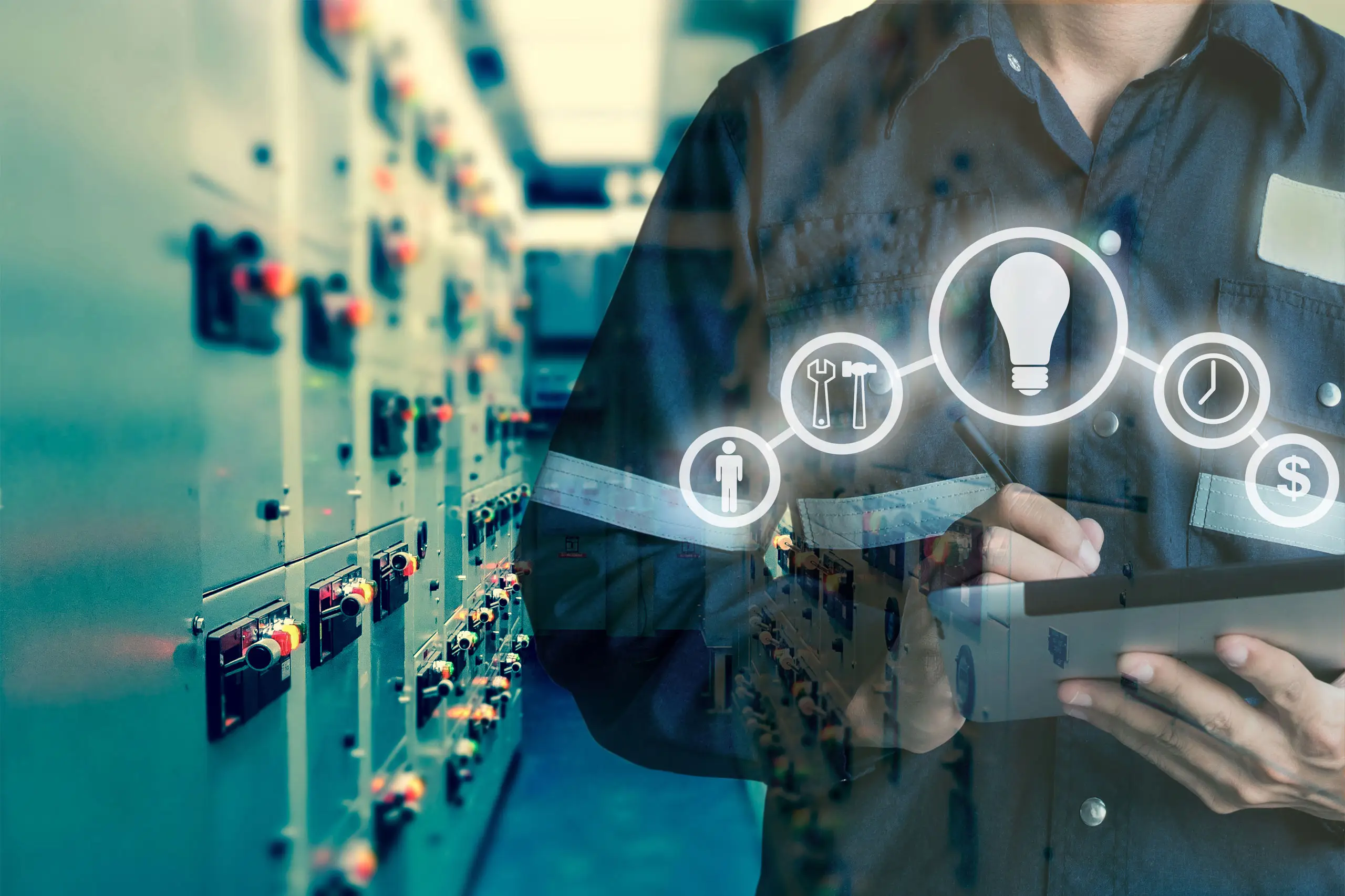
What is predictive maintenance (PdM)?
Predictive maintenance (PdM) is an asset management strategy that uses data analysis to identify potential anomalies with equipment before a failure occurs. PdM is the process of collecting data, analyzing data, and generating alerts related to anomalies. It enables proactive maintenance, minimizes the need for unnecessary preventive maintenance, and helps to avoid unplanned downtime.
How does predictive maintenance (PdM) work?
Predictive maintenance works by utilizing real-time data from assets to determine patterns and trends collected from sensors and historical records to identify operational problems and potential equipment defects before they happen. Alerts generated can be sent in various ways, such as SMS, email, or push notifications. When a potential problem is identified, PdM systems highlight the anomaly, which helps maintenance personnel implement the appropriate action to prevent equipment failure, power outages, and unplanned downtime.
Data can be collected from sensors installed in critical assets for different types of predictive maintenance, including:
- Thermographic analysis: When equipment has a fluctuating (especially rising) temperature, it may indicate an impending failure. Temperature sensors are used to monitor for a rise in temperature within critical electrical equipment, which can be caused by faulty connections, faulty cooling systems, and a range of other issues that can lead to catastrophic failure.
- Sound analysis: Sensors can be used to monitor the sound level of pumps or identify defects in products or manufacturing processes.
- Vibration analysis: Vibration sensors are used to measure the vibration frequency of bearings or shafts. They are also suitable for any rotating piece of equipment.
Predictive maintenance software generates notifications by monitoring the health of assets and informing personnel about anomalies in the data. This drives more effective and efficient maintenance programmes.
How does predictive maintenance help industries?
Predictive maintenance delivers efficiencies by identifying potential equipment issues in advance of failure in many industries, such as:
- Manufacturing: PdM monitors manufacturing equipment such as engines, robots, and conveyor belts to identify problems before a failure occurs.
- Healthcare: PdM monitors medical equipment, including ventilators and MRI machines.
- Transportation: PdM monitors vehicles, aircraft, and other transportation equipment.
- Power generation: PdM monitors power generation equipment such as turbines, motors, transformers, and generators to ensure safety and efficiency in power generation.
- Mining: PdM helps to monitor mining equipment, including excavators, and for operational and productivity increase.
- Oil and gas: The oil and gas industry relies strongly on the healthy operational status of equipment such as pumps, compressors, and pipelines, which PdM can monitor to prevent spills and other severe environmental hazards.
Benefits of predictive maintenance
Predictive maintenance, as opposed to preventative maintenance, ensures equipment that could be compromised and requires maintenance is only stopped before a failure actually occurs. This provides several benefits, including:
- Saves costs: PdM cuts down on unnecessary maintenance and saves costs over time in several ways:
- Reduces the amount of time spent on unnecessary equipment maintenance.
- Lowers the need to replace components, equipment or machinery.
- Minimizes the number of hours lost to maintenance and the need for manual inspection. - Reduces unplanned downtime: Predictive maintenance helps to reduce unplanned downtime by lowering the risk of unexpected equipment failures or the need to shut down equipment for maintenance. This helps to save costs and increases customer satisfaction through the provision of a more reliable service.
- Increases equipment lifespan: Predictive maintenance helps identify potential issues before they occur, allowing for the implementation of the most suitable maintenance approach. With insights from predictive maintenance, measures can be implemented to solve the specific issue rather than react speculatively, or worse, retrospectively following a failure. Identifying the root cause of a potential electrical failure and remedying the problem will also increase the lifespan of equipment over time.
- Improves personnel safety: Potential issues that could be hazardous can be prevented by the early identification of anomalies protecting personnel and property. Sensors monitor irregularities, detect anomalies when present, and generate notifications to help prevent hazardous incidents. PdM also provides opportunities for extra safety training as deemed fit. For example, where a particular piece of equipment has a high failure rate, PdM data provides insights to develop targeted safety training to help properly maintain the equipment.
- Provides actionable insights: Managing and planning scheduled or periodic maintenance tasks can be risky because sometimes equipment could break down before the next scheduled maintenance routine. Predictive maintenance is a data-driven maintenance approach that relies on collected data analysis on equipment health to identify impending anomalies. The insights from these data provide root cause analysis beyond reactive strategy that helps personnel implement appropriate actions for equipment optimization.
The differences between predictive maintenance and preventive maintenance
Whilst predictive and preventive maintenance aim to achieve similar objectives, both are two distinct maintenance approaches that have different techniques, benefits, and methods. The table offers comparisons between both maintenance approaches:
Predictive | Preventive |
|
|
|
|
|
|
|
|
|
|
Many organizations combine the implementation of predictive and preventive maintenance. As outlined above, predictive maintenance provides a broader range of benefits than preventive maintenance, leading to an increase in the implementation of PdM practices across many industries.
Organizations have identified the need to be proactive in critical equipment maintenance because of the risk of failures and associated negative outcomes that occur from reactive maintenance practices.
Predictive maintenance reduces the likelihood of equipment damage and helps prevent unplanned downtime by enabling organizations to repair assets before a problem occurs. Sensors can predict when equipment is likely to break down, and software provides actionable insights to analyze data for appropriate maintenance action. This prevents unnecessary maintenance, reactive action with negative repercussions and unnecessary downtime from equipment shutdown.