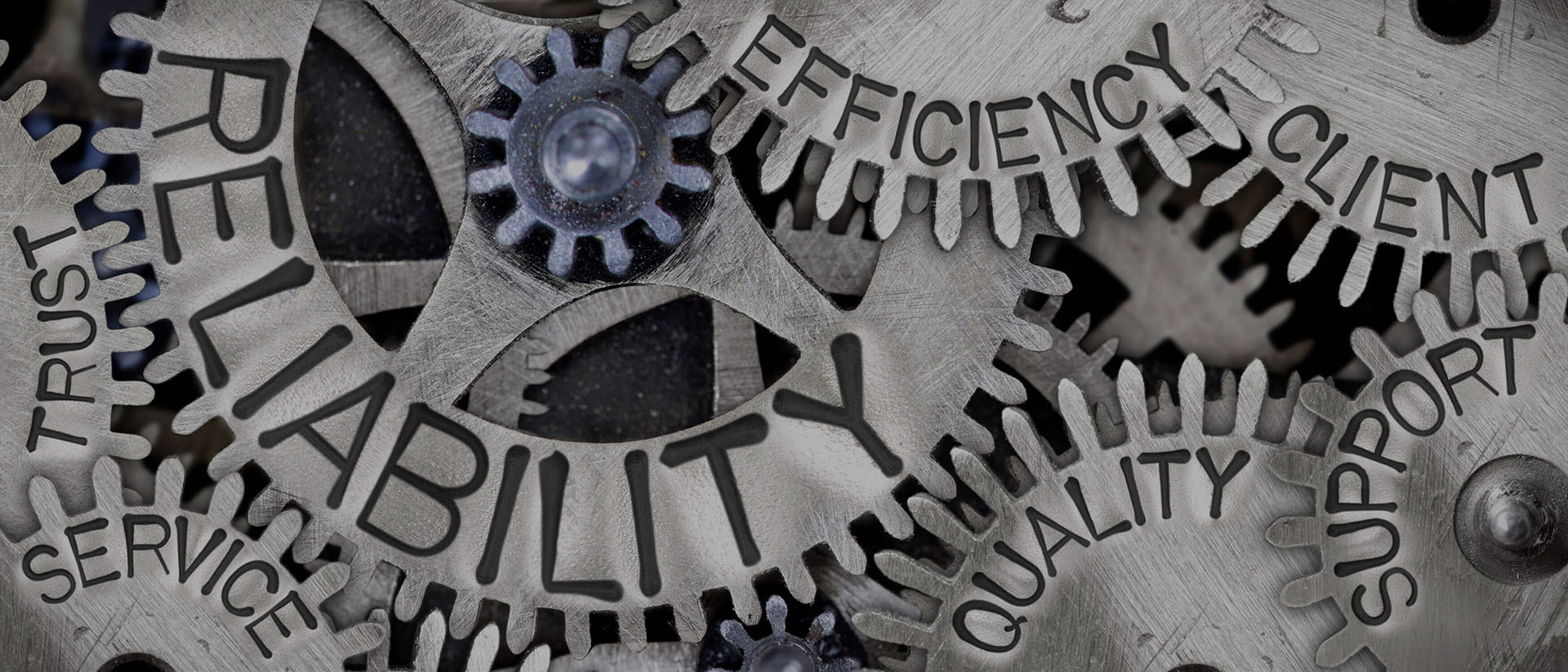
No matter what the industry, the reliability of electrical equipment is essential for the cost-efficient operation of the business. Equipment which causes power outages can result in millions of dollars in lost production downtime or pollution or cause serious injury or fatality to those in proximity to the failure.
A common cause of electrical outages is bad joints/terminations. These can be caused by several factors, including the thermal dynamics of load being switched on/off, causing the joint to expand / contract and over time become loose, human error by incorrect tightening, etc.
The method of detection has previously been periodic (normally annual) thermal inspections using a thermal imaging camera. However, one day per year is just a snapshot in time and represents less than 1% of operational uptime in a 24×7 industry.
The reliability of such inspections to deliver a common standard of fault detection was quite poor since it is invariably dependent upon the quality of the thermal camera and the operator's skill. In addition, the inspection report issued would rarely take into account the load on the circuit and could not be integrated as data into the SCADA/DCS/BMS systems of the client.
The Exertherm thermal condition monitoring system provides an unrivalled level of reliability in fault detection and the durability of the sensors. This is essential, as the sensors will be installed inside electrical switchgear enclosures/MCC drawers (buckets), with the intention that it is no longer necessary to perform periodic intervention maintenance on bus joints/cable terminations because you have the thermal condition data obtained via the sensors.
If sensor technology requires any maintenance or even replacement during the life of the electrical equipment in which it is installed, this is building in significant additional labour/parts/ production downtime cost for the end user client. There are wireless energy harvesting sensors out there which, according to their manufacturer product manual, will require intrusive (e.g. require shutdown of equipment) maintenance every two years! That equates to an extra 12 shutdowns (with all the associated costs), during the life of the equipment.
Another issue which is a “hot” topic is the use of wireless sensors to detect faults / acquire condition data. In many cases ( e.g. SAW technology), these “wireless sensors only have a transmission distance of approx. 30cm to an antenna. You will, therefore, need 2-3 antenna in a column of LV/MV switchgear ( they don’t fit in MCC drawers ). The antennas are hard-wired! So, the claim of being a wireless system is somewhat exaggerated.
However, the key point is that Exertherm has over 150,000 sensors successfully installed worldwide. They are completely passive and require no external power, and they come with a Lifetime Warranty / Zero Maintenance level of reliability, which avoids any future costs incurred with less reliable sensor technologies.
The increasing adoption of IIOT is accelerating the move from periodic inspection maintenance to condition monitoring. Thus, the choice of sensor technology is equally important to the decision to move to monitoring – selecting the wrong technology which cannot guarantee the same level of reliability as Exertherm, could be a strategic investment mistake.