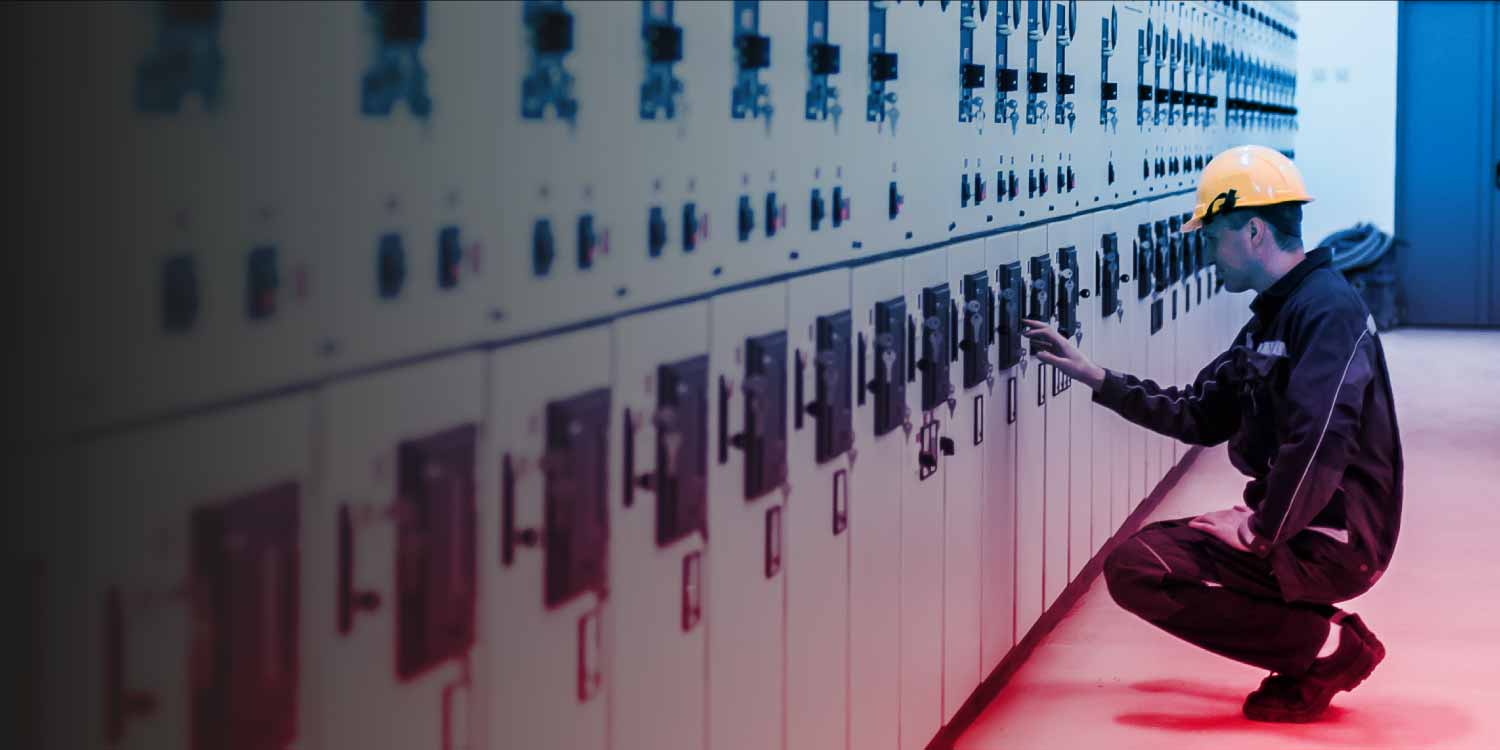
What is thermal monitoring?
One of the major causes of fire in electrical equipment is faulty joints or connections, where an increase in temperature is the primary symptom and an indicator that a potential problem could occur. Thermal monitoring enables organizations to detect the symptoms in those joints or connections that without intervention could otherwise lead to electrical outages, or worse, a fire.
Without early identification, the deterioration of faulty electrical joints or connections will lead to increased resistance and higher temperature, which will eventually result in thermal runaway and ultimately, a complete failure. Arc flash and fire, or even an explosion might occur, causing unexpected plant downtime or potentially leading to catastrophic consequences such as total equipment destruction or even personnel injury.
Continuous thermal monitoring is the next technology step from periodic infrared inspection:
- Permanently installed sensors inside electrical equipment provide 24/7 protection
- Delivers real-time, integrated temperature data for critical electrical assets
This enables electrical maintenance teams to predict failures, safeguard electrical equipment, and optimize performance. With the disruption to power supply posing an increasingly critical threat to organizations, the requirement for innovative thermal monitoring solutions for industry to maximize uptime through the prediction of faults before they occur. Additional benefits delivered by this technology include increased personnel safety and extended asset lifespan.