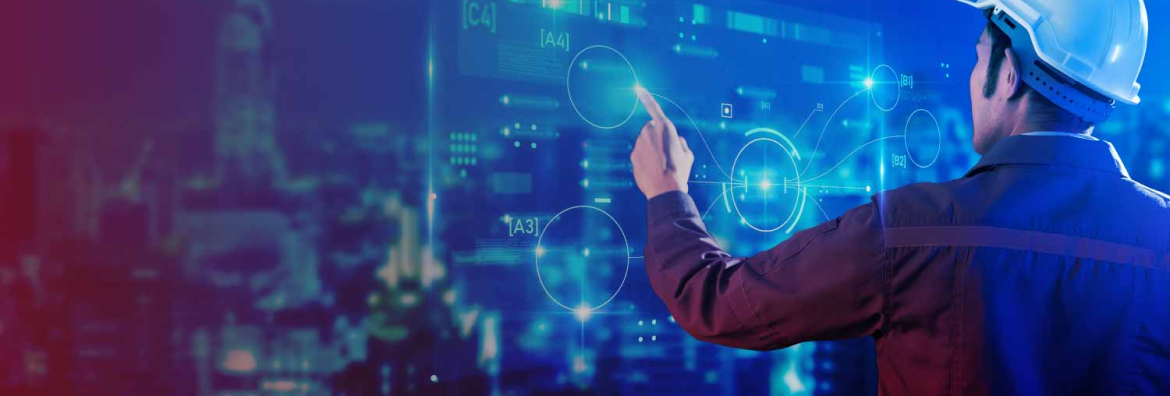
What is unplanned downtime?
Unplanned downtime is an unanticipated disruption or breakdown of a machine or process that halts the operation of a business, resulting in lost productivity, additional costs, and lower customer satisfaction. Several reasons, including equipment failure, power outages, natural disasters, or human error, can cause it.
What causes unplanned downtime?
Unplanned downtime can seriously affect a company's operations and bottom line; however, there are proactive measures organizations can take to reduce the chance of downtime and guarantee smoother operations by identifying potential sources of risk, such as the following:
1. Equipment failure: This is the most common cause of unplanned downtime. It can be caused by a variety of factors, including:
- Wear and tear: Over time, all equipment will wear down and eventually fail. This is especially true for heavy-duty or harsh-environment equipment.
- Misuse: If equipment is not used correctly, it can fail. Overloading the equipment, using it in an inappropriate area, or failing to follow the manufacturer's recommendations are all examples.
- Natural calamities like storms, floods, and earthquakes can damage equipment, resulting in unanticipated downtime.
- Defects: In rare situations, equipment may fail because of a manufacturing flaw. This is frequently due to a flaw in the design or materials used in the equipment's construction.
2. Power outages: Power outages can interrupt the operation of any business or system that relies on electricity. They can occur for a variety of reasons, such as:
- Maintenance: Power outages can occur during routine maintenance.
- Human error: Human error can cause power outages, such as when a worker accidentally severs a power line or leaves tools inside or near assets.
- Inclement weather: Power outages can also be caused by inclement weather, such as severe rain or snow.
3. Human error: Another cause of unplanned downtime is human error. Errors made by operators, technicians, or maintenance employees are examples of this.
- Configuration errors: These can include wrongly configuring settings, installing the wrong software, or connecting devices incorrectly.
- Errors in operation include operating equipment incorrectly, failing to follow protocols, and making blunders while debugging problems.
- Maintenance errors might include failing to perform equipment maintenance, employing the incorrect tools or techniques, or making mistakes while fixing equipment.
- Documentation errors might include missing or incorrect documentation, missing or outdated processes, or imprecise directions.
Difference between planned and unplanned downtime
The difference between planned and unplanned downtime is centered on how they both impact the availability and dependability of a system or piece of equipment.
Planned downtime
Planned downtime occurs when a system or piece of equipment is taken offline for scheduled maintenance, upgrades, or other tasks. Organizations can carry out normal maintenance, upgrades, or repairs during planned downtime without significantly impacting business operations. To reduce potentially negative knock-on effects, planned downtime is often scheduled and communicated to stakeholders. Employees and consumers can plan for this type of downtime because it is usually publicized in advance.
Unplanned downtime
Unplanned downtime is unexpected and can occur anytime, whereas planned downtime is scheduled and anticipated. Unplanned downtime is unanticipated and can be caused by various circumstances, including hardware failure, software problems, or natural calamities. This type of interruption can be more costly and disruptive to organizations than planned downtime.
Cost of unplanned downtime
Unplanned downtime can have significant cost implications in lost revenue and reduced productivity.
The Ponemon Institute found that the average cost of unplanned downtime in data centers is now $7,900 per minute, up from $5,600 per minute in 2010. The cost of unplanned downtime varies depending on various factors, including the industry, the firm's size, and the outage duration. However, the following are some of the most general costs associated with unplanned downtime:
This indicates that one hour of downtime can cost a company more than $600,000.
- Revenue loss: When a business is closed, it cannot earn revenue. This might result in severe income loss with customers moving to competitors, particularly for enterprises that rely on a continuous 24x7 supply to consumers.
- Lost productivity: Employees cannot be productive when a business is closed. This can result in a loss of output and efficiency, which can harm the bottom line.
- Customer dissatisfaction: Customers become unsatisfied if they are unable to obtain a company's products or services. Customers and corporate reputation may suffer as a result.
- Increased costs: When a business is closed, it may incur increased costs. This could include the expense of recruiting temporary workers, paying for overtime, or making emergency repairs.
How to measure unplanned downtime
The formula for calculating unplanned downtime using a time measure is:
- Unplanned Downtime = (Time Asset is Down / Total Time) x 100
If the cost of overhead and other factors are taken into account, other things might easily increase the overall cost of unplanned downtime.
How to reduce unplanned downtime
Unplanned downtime can be expensive and disruptive to organizations. The likelihood of reducing unplanned downtime (even in emergency situations) is much higher when organizations adopt a proactive approach. This can involve carrying out the following measures:
- Inspect and maintain equipment regularly. This will help identify and resolve potential faults before they cause downtime.
- Prepare a backup strategy. Creating disaster recovery plans can help mitigate the impact of any unplanned outage.
- Training personnel in emergency protocols and procedures. Employees should be trained on how to prevent and respond to unplanned downtime. Implementing standard work procedures can prevent variances that could result in downtime. Consistency, efficiency, and error reduction are all enhanced by standardizing operator actions, processes, and best practices. Training and standardization can reduce downtime and mitigate the impact of downtime if it occurs.
- Performing process audits. Procedures must be optimized to reduce unplanned downtime. Process audits reveal areas that can be improved, reducing or eliminating the causes of unplanned downtime. Organizations should perform routine downtime analysis to spot trends, underlying problems, and recurrent problems. Targeted solutions can then be applied, and preventive measures can be implemented as a result of understanding the root causes of downtime.
- Make use of predictive maintenance. Condition monitoring is used in predictive maintenance to identify potential faults before they lead to unplanned downtime. Analyzing sensor data in a software platform will provide real-time actionable insights and trends. Instead of relying solely on instinct, this enables organizations to make better-informed decisions, helping save money by reducing the frequency and duration of outages.
While downtime in an organization is a fact of life, management, operators, and technicians work tirelessly to minimise it and its repercussions. Unplanned downtime still costs organizations a significant amount of money, lost productivity, and reputational damage when it occurs. This can be significantly reduced by implementing measures that increase operational efficiency, reduce downtime, save money, and preserve customer satisfaction.