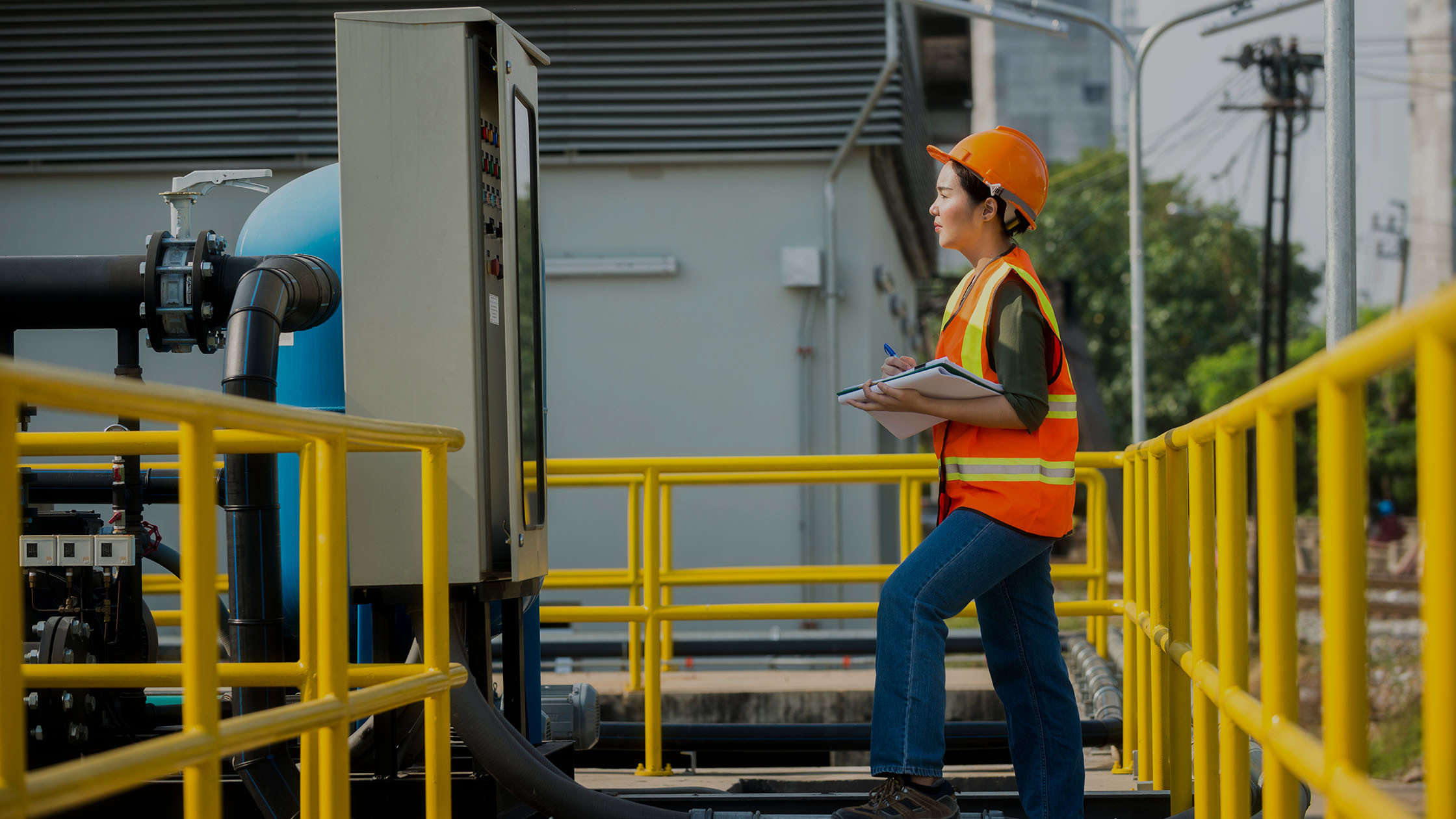
There are a few examples of technology which should be broadly adopted but, for various reasons, take time to be accepted. The concept of future-proofing — hedging against the risk of not adopting a future technology — is highly relevant to the water industry’s approach to the problem of ageing electrical infrastructure.
The risk of doing nothing is substantial, given the pace of technological change that we’re all living through right now.
According to the US Infrastructure Report Card, water service disruptions cost billions, yet the burden of disruption due to power failure could be reduced by integrating sensor technology.
Aeration and pumping are intensive processes in water/wastewater treatment. The prevalence and variety of these motor-driven pumps and machinery in a water plant make the electrical system critical to operations. The power to all motors is managed by motor control centers (MCCs), the health of which is vitally important to ensure uptime for critical processes.
Motor Control Centers (MCC) are known to be prone to failure caused by loose or compromised connections. The joints most susceptible to faults are typically at the rear of the MCC bucket and cannot normally be accessed for inspection without de-energizing.
These bad joints/terminations can be caused by a number of factors, such as thermal dynamics of load being switched on/off causing the joint to expand/contract and become loose over time, and human error by incorrect tightening, etc.
While periodic electrical safety inspections can assist in identifying these deficiencies, they are typically only carried out annually and provide none of the ongoing benefits of 24x7 condition monitoring.
Since heat is often an early indicator of degradation, Exertherm’s thermal monitoring allows operations to capture baseline data and identify abnormal temperature patterns before electrical failure occurs. Thermal monitoring from Exertherm provides accurate data that enables you to quickly pinpoint faults, accurately predict what you need for the next scheduled plant shutdown for smart maintenance, and reduce other electrical safety issues that may put staff at risk from electrical hazards.
Reasons to adopt predictive asset management and smart sensors for electrical infrastructure:
- Increased facility uptime - sensors enable the prediction of faults and improve cost efficiency while reducing the risk of environmental impact, providing increased asset and facility uptime improved cost efficiency.
- Increased facility safety - A treatment plant operator’s duty is to ensure the safety of all employees and contractors. Exertherm removes the need for exposure to energized equipment for the purpose of condition assessment.
- Increased fault detection - Exertherm monitors 24x7 / 365 = 100% of uptime. Annual thermography inspection is one day out of 365 = <1%. This means a high dependence on luck to detect a failure in advance.
- Integrated Data - Exertherm utilizes industry-standard Modbus protocol, enabling simple integration into any BMS/SCADA. Data from annual thermal inspections are unsuitable for direct integration into SCADA/BMS and cannot provide alarm notifications, trending, analysis, etc.
- Increased Reliability - Exertherm sensor technology produces data of a consistent, accurate and uniform quality, which is essential when Go vs. No Go decisions must be made. Thermography inspection temperature measurements depend highly on the quality of the thermal camera and operator and the age and quality of thermal windows if installed. Thus, data produced is not of a uniform quality.
- Cyber Security - Exertherm sensors are hard-wired and, therefore, avoid the acknowledged cyber security risk which exists with wireless sensor technology.
- Future Proof Solution - The IIoT (Industrial Internet of Things) “revolution” is globally transforming how electrical infrastructure is procured, operated, and maintained in the water/wastewater industry.
- Installing Exertherm sensors to create the data of uniform quality for subsequent analysis is a key part of the IIOT jigsaw since NO SENSOR = NO DATA!
- Proven Acceptance - ALL major OEMs now advocate using thermal condition monitoring over periodic inspection.
Learn more about Exertherm's Mission Critical award-winning Motor Control Center Solutions.