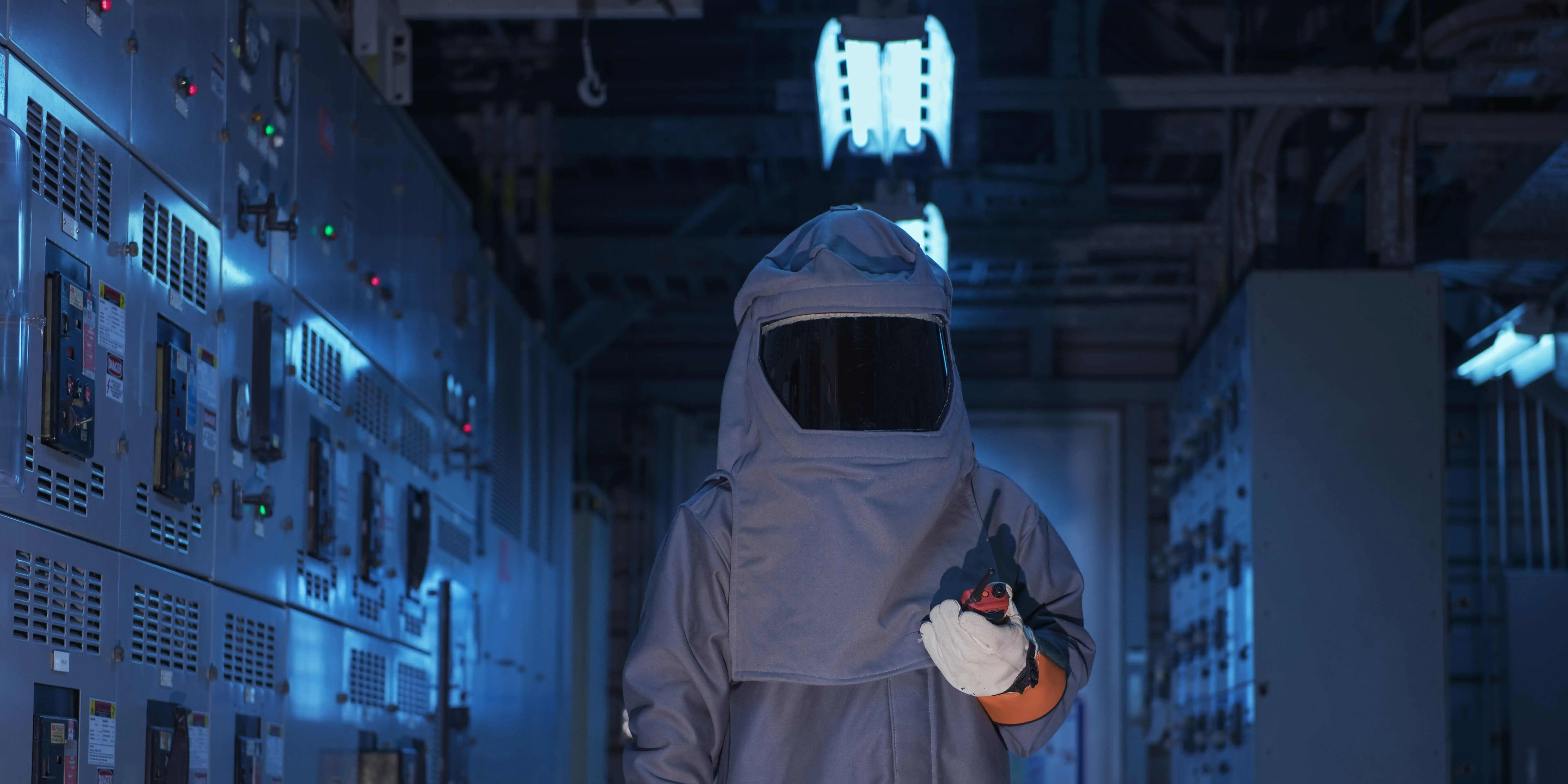
What is an arc flash?
An arc flash is a sudden, explosive release of energy that results from an electrical fault or short circuit within an electrical system. In other words, an arc flash is when an electrical current flashes over and goes from one conductor to another or the ground instead of following its original route. An electric arc forms between two conductive objects during an arc flash event, usually due to a breakdown in insulation or the presence of conductive material.
When there is a rapid expansion of air and vaporized material from an arc flash, an arc blast may occur. The arc creates a dangerous and highly volatile scenario by intensely releasing heat, light, and pressure. When workers are exposed to an arc flash, they can be exposed to temperatures of up to 35,000 degrees Fahrenheit.
Arc flash incidents pose a serious risk to workers and can cause severe injuries and fatalities, as well as significant property and equipment damage. To reduce these risks, it is essential to have a thorough understanding of arc flash and put appropriate safety precautions in place.
Arc flash vs. arc blast
The difference between an arc flash and an arc blast is that they are both separate by-products of massive electrical explosions, even though they are sometimes used interchangeably. The two are often treated separately because they are technically different concepts
An arc flash is the light and heat produced as part of an arc fault, a type of electrical explosion.
An arc blast is the pressure wave that follows when an uncontrolled arc event vaporizes the metal conductors. Arc blasts are typically less severe than arc flashes but cause equally as much damage and injury as arc flashes.
With personnel safety being a high priority for every industry, it is essential to protect workers from arc flash and arc blasts by identifying potential hazards as early as possible and taking vital steps to mitigate the risk of injury.
Causes of arc flash
Factors such as equipment failure, poor maintenance, human error, or external elements can cause arc flash incidents.
The following are typical arc flash causes:
- Equipment Failure: Arcing caused by loose connections, defective insulation caused by aging, or poorly maintained electrical components can force an energized conductor to come into contact with another conductor, resulting in an arc flash incident. For example, overloading equipment can cause insulation to overheat and break down, which can lead to arc flash.
- Human Error: Personnel who work near energized electrical equipment should be trained on the risks and prevention of arc flash. Improper work practices, inadequate training, improper installation, or failure to comply with safety measures can accidentally cause electrical faults and arc flash incidents.
- Environmental Factors: Environmental elements must be understood because they can result in an arc flash. These elements, such as weather-related dust, moisture, condensation, or conductive objects close to electrical systems, can further increase the likelihood of equipment failure and contribute to arc flash occurrences.
The effects of arc flash
Arc flash incidents can have some severe effects on people and equipment. For example:
- Human Injury: Humans close to an arc flash may sustain severe burns, respiratory injuries, hearing loss, and vision impairment due to an arc flash's intense heat and blinding light. The severity of human injury can be determined by the proximity of humans to the hazard, the time of circuit to break, and the temperature.
- Equipment Damage: Arc flash incidents have the potential to seriously damage electrical systems, causing unplanned downtime, expensive repairs, and the need for equipment replacement.
- Fire Hazards: Arc flashes can set fire to nearby flammable objects, leading to secondary fires, therefore increasing the risk to people and property.
Implementing arc flash safety measures
Deactivating compromised equipment is the simplest and safest technique to completely remove the possibility of an arc flash or electrical shock.
The following preventive measures should be put into practice to increase workforce safety and reduce the likelihood of arc flash incidents:
- Risk Assessment: Conducting a comprehensive analysis of electrical systems is essential to identify potential arc flash hazards, assess the severity of risks, and determine the appropriate safety measures. Risk assessment helps put in place control measures to mitigate the risk by eliminating the hazard, reducing the hazard by installing arc flash barriers or improving maintenance procedures, and controlling the hazard with the use of appropriate PPE or by implementing lockout/tagout procedures.
- Electrical System Maintenance: Regular inspection, testing, and proactive maintenance of electrical equipment helps to identify and address potential issues to prevent arc flash incidents.
- Personal Protective Equipment (PPE): The appropriate PPE depends on the level of risk, but it typically consists of arc flash suits, flame-resistant clothing, insulated gloves, face shields, safety glasses, head protection, footwear, and hearing protection. These items help to protect personnel working near potential arc flash hazards.
Here are a few ways to select the appropriate PPE for arc flash:
- Consult a safety expert: Assistance from a competent safety professional in choosing the PPE that would best meet your needs is a helpful measure.
- Identify the degree of risk: The quantity of PPE needed will depend on the level of risk.
- Verify the Arc Thermal Protection Value (ATPV) score: ATPV represents the incident energy level, measured in calories per square centimetre (cal/cm2), at which a fabric or material has a 50% chance of averting a second-degree burn when exposed to an arc flash. The thermal energy that the PPE can withstand before it breaks down should be measured by the ATPV rating.
- Ensure that the PPE fits comfortably. The PPE should fit comfortably without being overly tight.
- Regular PPE inspection: A regular inspection should be made for wear or tear on the PPE.
- Engineering Controls: Implementing engineering controls is an essential element for workspace safety, as it focuses on hazard prevention at the source. Engineering control reduces the likelihood and impact of arc flash incidents through equipment modifications, condition monitoring, current-limiting fuses, arc-resistant switchgear, enclosures, and automation. Once implemented, these solutions can provide a long-term solution requiring less human contact with electrical systems.
Other forms of engineering control can include:
- Training and Awareness: Workers should be informed about the dangers of arc flash, safe work practices, and emergency response protocols through appropriate training programs.
- Arc Flash Labels and Signage: Labelling electrical equipment with arc flash hazard warnings and safety instructions ensures workers know the potential risks and the appropriate precautions they need to take.
- Compliance with Standards: Following relevant industry standards and regulations, such as NFPA 70E, OSHA, and IEEE, ensures compliance with safety guidelines and best practices.
Arc flash incidents pose a serious threat to workers, equipment, and the overall safety of the workplace. Organizations can actively reduce these risks by learning about arc flash's origins, consequences, and preventive solutions. Thorough safety processes should be implemented to mitigate risks and avoid arc flash incidents. These processes include adequate personnel training and the enforcement of safety regulations. In summary, arc flash safety must be prioritized if a safe and effective workplace is to be maintained.