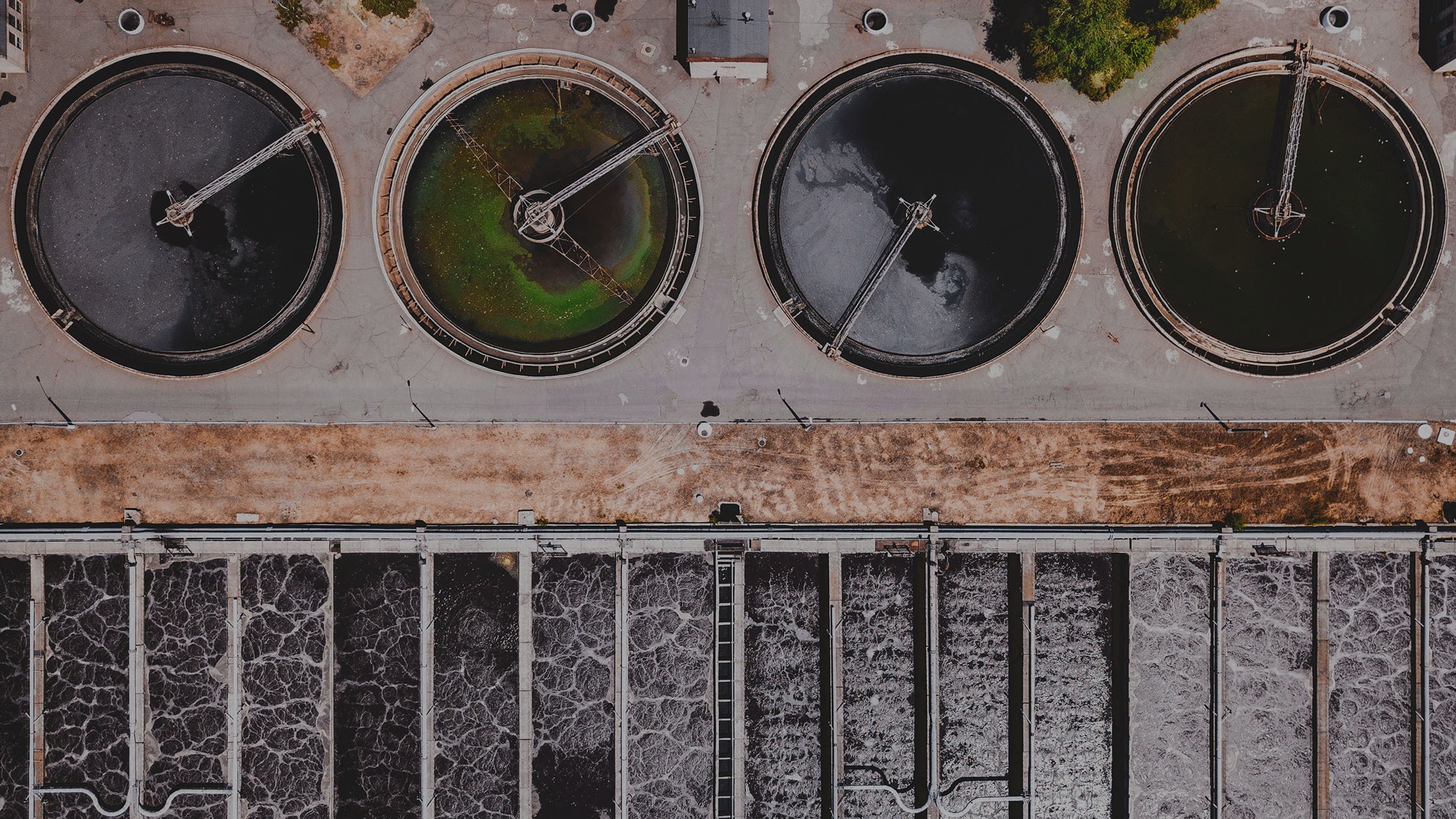
It's time to challenge preconceived notions and assumptions of electrical infrastructure operations & management.
Globally, engineering and operations for water and wastewater organizations are facing financial and environmental challenges from:
- Demands to maximize the life and value of capital assets
- Requirements to run operations and maintenance resources with tighter budgets
- Risks of liability/penalties for any environmental destruction from effluent discharge as well as reputational damage
In America, the new administration is prioritizing the nation’s ageing infrastructure within water and wastewater; it's clearly calling for an upgrade and investment in new technologies to support disadvantaged communities, as well as those areas undergoing exponential growth in population that significantly impacts the existing water, sewer, and wet weather management systems due to the expansion needs.
Recently the Senate passed the United States Drinking Water and Wastewater Infrastructure Act; this certainly could be the much-needed financial injection that owners, operators, and managers of water and wastewater systems require to face the increasing challenges of doing more with less head-on. But will drinking water & wastewater infrastructure problems stand the wait while the law-makers scrutinize and argue over the budget?
As far back as 2011, the American Society of Civil Engineers (ASCE) Failure to Act report highlighted the precarious timeline left on ‘useful lives’ of water and wastewater system electrical components as found by the Environmental Protection Agency (EPA) in their Infrastructure Gap Analysis started in 2002.
Today, much of the electrical components supporting water and wastewater will be passed these ages! It is a simple fact that aged equipment which is beyond its nominal life expectancy will be prone to an increased risk of failure. The time for change is now. Power failures for water infrastructure can result in water supply disruptions and damage to other types of infrastructure as well as have a potentially devastating impact on the environment.
So how best to bridge strategy, technology, business process, engineering, and operations and maintenance?
One way to start is a tactical use of innovative sensor technology for electrical infrastructure that delivers these immediate tangible benefits:
- Ensures increased power reliability
- Reduces on-going maintenance
- Increases operational safety
- Maximizes the life and value of these assets
The industry can start by challenging preconceived notions and assumptions surrounding traditional Operations & Maintenance (O&M) models for their electrical infrastructure and make a shift towards more strategic predictive maintenance.
Typically, maintenance includes thermography inspections; often done by third-party contractors or conducted by in-house teams during a de-energized state unless assets already have infrared (IR) windows installed.
Yet these types of inspections on critical assets are periodic, and even with windows, can be impacted by:
- Degraded rates of IR transmission of windows material (up to 30%)
- Physical obstructions in the way of hard-to-reach crucial connections.
The accuracy of temperature data and building historical trends is paramount to catching issues early. Equally importantly, such thermal inspections tend to be carried out annually, which represents less than 1% of operational uptime – leaving 99% dependent on luck.
Faced with aging switchgear, transformers, and motor controls, along with the more regulatory push for arc flash studies, the question has to be raised: Is the whole nature of fly-by periodic inspection rigorous enough when it comes to electrical infrastructure? Why has the adoption of thermal sensors on this critical function lagged behind when it clearly offers increased safety, tangible OPEX savings, and reduced levels of failures (monitoring can detect up to 70% more failures than periodic inspections)?
There’s an opportunity to upturn periodic thermography inspections and move away from reactive maintenance
With the support of the Environmental Protect Agency (EPA), a third of water and wastewater utilities have already started their programs to develop and build an inventory to identify the operations and pieces of equipment in their facilities. Some utilities are already realizing the benefits of sensors and integrated instrumentation and controls - monitoring flow, levels, and bio-reactions. Monitoring electrical assets clearly needs to be on the roadmap for integration.
Moving to continuous thermal monitoring not only alerts engineering teams to potential damage and issues, but it’s a way to build a robust data set on electrical assets that will allow operations and maintenance to make smarter proactive decisions; long term these insights let organizations shore up their asset management programs to be more resilient and affordable.
Extending the life of these assets by purely retrofitting thermal condition monitoring to existing equipment and making sure that specification for new equipment follows suit, ensures that data is captured and can be included within an O&M program; no sensors=no data. But this simple installation can provide unprecedented visibility of assets in most need of intervention/mitigation and improves the risk management and resilience of the electrical infrastructure that powers pumping and treatment plants.
Looking to industry peers, adoption isn't complicated. One Exertherm customer took the prudent approach –Led by engineering, their team looked at the greatest likelihood of electrical asset failure and where they thought risk would occur. Presenting this outline with the accompanying consequences, the team got quick approval for a proof of concept they managed in-house. Now they are using the same approach to discern where to invest next to optimize the use of existing electrical assets. It’s easily broken down.
8 Step Electrical Infrastructure O & M model:
- Inventory electrical assets based on rehabilitation, repair, and replacement
- Identify the stakeholders affected by the asset
- Run a Proof of Concept (POC)
- Set management process and goals
- Create a new practice to make up “good” asset management
- Refine the asset management policies
- Write a set of asset management strategies
- Detail the tasks required to implement an electrical infrastructure program of improvements
Some of the Customer's process changes took immediate effect due to the pandemic. Downtime and de-energizing their pumping stations to allow for periodic inspection was always tricky for the safety of their personnel in the best of times but the added risk of COVID encouraged new ways of working.
Exertherm systems provide the ability for condition data to be integrated (using industry-standard comms protocol – Modbus) to front-end instrumentation & control software within a facility's network. In instances where aged equipment does not have comms capability, Exertherm’s standard option is an advantage; the HMI and LED displays allow for quick visual indication of the asset condition & alarm status. Having a fast, easy visual update on condition and local & remote alarm notifications delivered operations gains immediately to the Customer.
With Exertherm already in place from the POC, the customer’s engineering team was able to quickly pivot and minimize staff exposure by making regular inspection part of routine site visits without the need for shutdown. Where network comms was unavailable, the HMI allowed for effortless recording/reading of information from data cards to front-end software, swiftly and safely by one of the team.
The data collected in a short period gave engineering and operations the ability to remotely analyze, prioritize and justify work based on the likelihood and severity of the failure, providing immediate cost savings.
Longer-term, the engineering team knows the data set they are building will give them a better understanding of existing electrical system performance and condition. They have already been able to optimize infrastructure servicing through improved insight into asset conditions and are developing their planning tools to cover electrical components.
Whether drinking water and wastewater systems are publicly or privately owned, are aged or underfunded, clearly, the management of electrical assets should no longer be purely reactive.
For those looking to move away from traditional inspection, Exertherm solutions provide reassurance as our implementation is economical, fast, considers safety first, and was designed for operational flexibility and to fulfill future digitalization needs. Exertherm sensors also come with a ‘Lifetime Warranty’ which guarantees zero maintenance/repair or replacement / re-calibration, so ensuring there are no future in-built costs from installing sensors.
Data-driven insights on electrical assets—their condition, location, and real value—will help organizations make smarter, more cost-effective decisions to better understand their largest risks and avoid critical electrical failures that could put their water infrastructure at risk.